NEMA’s Evaluating Water-Damaged Electrical Equipment1, first published in 2004, contains excellent reference material to evaluate electrical equipment that has been exposed to water through flooding, firefighting activities, hurricanes, and other circumstances.
The document provides a table summarizing recommended actions for various types of electrical equipment to determine whether they need to be replaced or reconditioned. New technological solutions have been developed that provide a third option: the core device (e.g., power circuit breaker, motor control center enclosure) is replaced with an upgraded device that matches the original equipment’s mechanical and electrical interfaces. The upgraded device is consistent with new equipment Standards and technological advancements without disturbing the primary enclosure, incoming and outgoing cable connections, or operating controls.
The benefits of upgrading versus the traditional replacement option are:
- Costs for direct replacement upgrade devices are equal to or less than replacement equipment of the original design. The cost advantage is derived by the use of available manufactured components and devices versus tooling required to manufacture equipment which may have been in service for ten to twenty years or longer.
- Delivery is faster since the direct replacement devices are in-stock and the mechanical and electrical interfaces have been designed and stocked for common vintage equipment.
- New technology can be incorporated within existing structures at no added costs. Additional safety features can also be included to better address arc-flash concerns and personnel safety.
- Speed of remediation is greatly increased since complete removal of the entire electrical structure is not required, cables are not disturbed, and equipment upgrades can be completed in intervals—allowing for selected power restoration during the remediation process. For power circuit breakers or motor control centers, individual devices can be installed as remediation progresses.
- Long-term reliability is improved by adding optional system improvements during the remediation period and includes monitoring of predictive failure modes such as: humidity, temperature, dust, smoke, intrusion, vibration, floor water, power quality, or other parameters. For medium voltage equipment, continuous partial discharge activity can also be monitored. These reliability improvements provide for audible alarms, messaging (text, voice, and email), and also service dispatch, depending on the needs of the customer.
- NOTE: Water damage from any body of water is usually defined as “flood damage,” therefore an overhead steam or water leak can be defined as flood damage. Being notified of floor water and/or increasing humidity allows for immediate corrective actions, preventing subsequent electrical equipment failure.
- · Life-extension of existing capital investments is achieved due to the critical core components and devices being replaced with “new” devices.
The following are examples of categories within NEMA’s Evaluating Water-Damaged Electrical Equipment. Included is an upgrade option in addition to the replacement or recondition options. These solutions have been applied for past hurricanes and other flood conditions.
Motor Control Center Equipment
New technology motor control center equipment, commonly referred to as MCC inserts or buckets, can be equipped with mechanical and electrical interfaces to become direct replacements for many manufacturers’ motor control equipment.
Example Scenario
In October 2012, Superstorm Sandy battered the Northeast and many facilities suffered major damage. One major utility company lost an entire line-up of MCCs at one of its power generation facilities. The utility contacted a service group in New Jersey to get an assessment on replacement and upgrade capabilities. A NEMA member factory was able to supply replacements to the customer within days. Because the factory’s service group provided the installation and start-up, the down time suffered by the utility was dramatically shortened.
Power Equipment
New technology circuit breakers can be encased within a mechanical and electrical interface, including insulating bushing and electrical secondary controls, to provide for direct replacement to many manufacturers’ circuit breaker assemblies. These solutions apply to low voltage power circuit breakers (600V) as well as 5/15kV assemblies. Figure 1 illustrates an example of a low voltage power circuit breaker upgrade solution and Figure 2 illustrates an example of a 4.16kV or 15kV circuit breaker upgrade solution.
Section 4.3 in Evaluating Water-Damaged Electrical Equipment also discusses the potential for reconditioning of protective relays, meters, and transformers. A recommendation suggests contacting the original equipment manufacturer to ensure that all electronic protection and control functions have been fully restored. An upgrade option is also available for these applications since newer multi-function relays and metering can replace multiple traditional devices. The benefits described earlier concerning cost savings, speed of delivery, and improved technology also apply in this application. Figure 3 illustrates an example of an upgrade solution for relays, metering, and controls while maintaining the existing equipment structure.
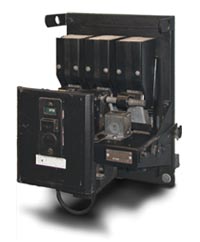 |
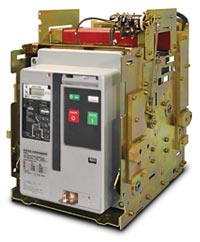 |
Original LV Circuit Breaker |
Current Manufactured
LV Circuit Breaker within Mechanical /
Electrical Interface for Direct Replacement |
Figure 1. Power Equipment—480V Circuit Breaker Upgrade Option
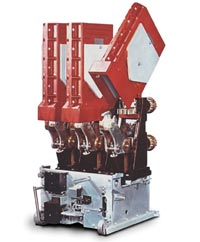 |
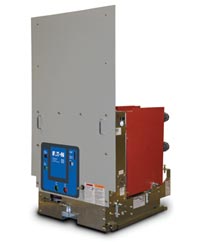 |
Original 15kV Circuit Breaker |
Current Manufactured
15kV Circuit Breaker within Mechanical /
Electrical Interface for Direct Replacement |
Figure 2. Power Equipment—5/15kV Circuit Breaker Upgrade Option
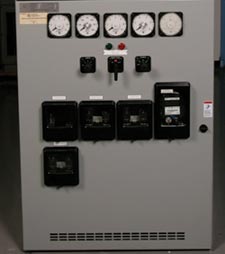 |
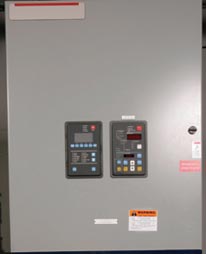 |
Original Relays, Metering and Controls |
Upgraded Multi-Function Relay, Metering,
and Controls |
Figure 3. Power Equipment—Protective Relay, Metering,
and Controls Upgrade Option
Next | Disaster Recovery Planning
Evaluating Water-Damaged Electrical Equipment, National Electrical Manufacturers Association (NEMA), 2004