This piece was originally published in the September 2018 issue of electroindustry.
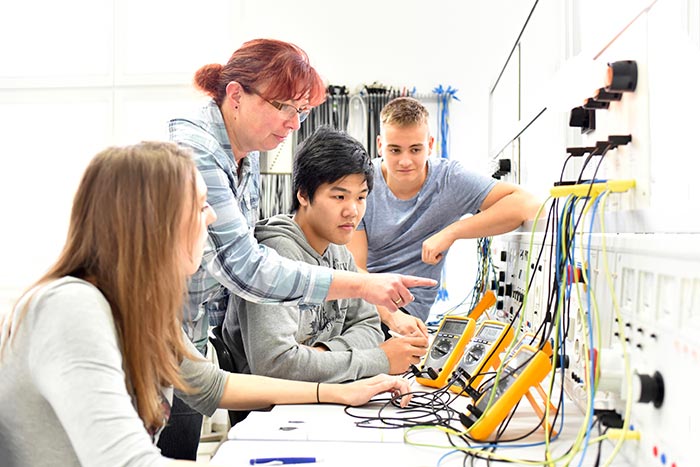
Jonathan Stewart, Industry Director, Utility Products and Systems Division, NEMA
In 2018, NEMA set out to tackle the workforce development gap through three projects under the Workforce Development Strategic Initiative. They involved a curriculum sharing feasibility study, an industry promotion digital toolkit, and an industrial maintenance technician youth apprenticeship.
The digital toolkit and apprenticeship program will be rolled out at the Workforce Development Seminar on Wednesday, November 14, which will be held in conjunction with the NEMA Annual Meeting. For more information, visit www.nema.org/workforce-development-seminar.
In a study conducted by Tooling U-SME, the feasibility of curriculum sharing was determined to be constrained because of challenges related to recruiting and training instructors, capital investment to procure requisite training equipment, and non-alignment of curriculum Standards from state to state.
To create an industry promotion digital toolkit, NEMA retained Edge Factor, a communications firm that specializes in promoting the manufacturing sector. It created a series of videos and other digital tools to raise awareness of the electroindustry and demonstrate its viability as a safe, innovative, and dynamic career pathway for middle and high school students. The firm developed a Netflix-style dissemination platform that NEMA Members can use to run the videos and activities while tracking post-event hits and other metrics.
NEMA also retained Tooling U-SME to develop an apprenticeship program for high school students to gain hands-on experience as industrial maintenance technicians. Tooling U-SME worked closely with a group of NEMA Member representatives from human resources and technical backgrounds to develop the program. The apprenticeship will have five domains, each with a respective curriculum and on-the-job training component: safety, electrical knowledge, mechanical repair, production equipment, and manufacturing aptitude.
Once developed, NEMA Members will be able to adopt and adapt the program to meet their local needs as well as their level of resources. Tooling U-SME will develop the curriculum, an on-the-job training guide, and a “train the trainers” handbook.