This piece was originally published in the August 2018 issue of electroindustry.
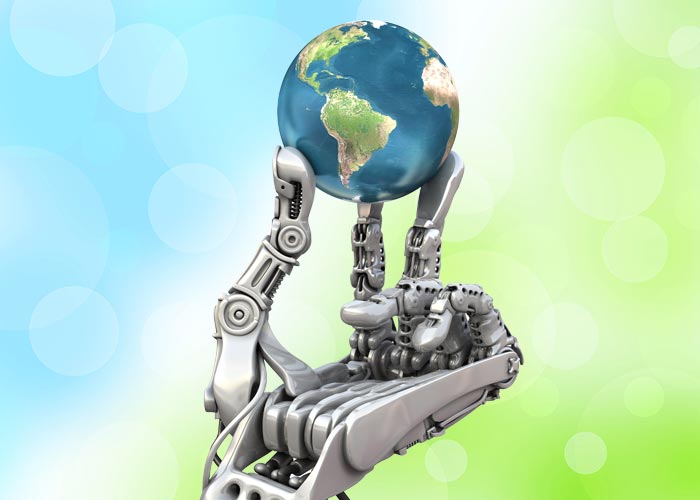
Kirk Anderson, Industry Director, Industrial Products and Systems Division, NEMA
Prior to joining NEMA, Mr. Anderson served in roles of principal engineer and business development manager for motors and generators at UL. He was named the first IEC motor energy efficiency expert in 2016.
In the decades since the oil crises of 1973 and 1979, countries around the world have been looking for ways to save energy.
Energy savings often start with motors. They are the invisible force behind the compressors in our HVAC systems, the pumps providing water to our homes, and fans of every sort. They make up a vast majority of electrical energy used for industrial applications, with some estimates as high as 70 percent, and roughly 40 percent for all electricity consumed. Because of this, most of the initial efforts to reduce energy usage were focused on improving the efficiency of the motor.
When the original energy-efficiency regulations and Standards were developed, the efficiency was measured at a single point. This makes sense if the product is operated continuously at its rated design point (100 percent).
When Efficiency Is Not Efficient
NEMA introduced high efficiency (~1990) and later (2001) NEMA Premium® energy-efficiency motors programs. These are roughly analogous to IE2 and IE3 efficiency classifications, respectively. While this resulted in significant improvements in energy efficiency, the quest to save energy continued. Unfortunately, we have come to the point where simply increasing the efficiency of the motor can significantly increase the cost to build it, but with little real energy savings.
Unless significant redesign takes place in the final application, retrofitting an existing application with a newer high-efficiency motor can result in no energy savings. The reason for this is that higher efficiency motors have higher base speeds. If the motor is operated below 100 percent load (which is often the case), the increased rotational speed results in increased energy being consumed.
If simply replacing an old motor with a higher efficiency motor isn’t the solution, what is?
To answer this question, we need to look at two characteristics that can result in significant energy savings: shifting the focus to the overall efficiency of the system and use of motors with variable speed capability.
Overall System Efficiency
Take, for example, a 10 hp motor. The efficiency rating of a Standard efficiency motor (IE1) is 86 percent; a NEMA Premium efficiency (IE3) motor is just over 90 percent. Gears are commonly used with motors and affect the overall efficiency of the system. A low-cost gear may reduce it in half. Conversely, using the best gear might only affect the system efficiency by a couple points. Knowing this, it’s easier to see that looking at the system might result in greater energy savings than simply focusing on the motor.
To better understand this concept, consider if your car’s engine only operated at optimum efficiency (e.g., 55 mph). The only way to adjust the overall speed of the car would then be to use the brakes. You can imagine how much energy would be wasted sitting in traffic while the brakes kept the car stationary and the engine continued to work at the same output. This is how traditional energy efficiency was measured: at a single (fixed) point, without regard to real-world variability.
Obviously that would be a car few people would want to drive. This is where system efficiency helps.
System efficiency takes a broader view and tries to look at the overall installation. By evaluating the overall system, incorporating the variability of loads, and determining how long the application operates at each point, the designer can incorporate variable speed technology or otherwise optimize the design to maximize energy savings. This benefits the user, since this often translates into real energy savings.
In a system efficiency world, our car would now have an adjustable gas pedal that can vary the speed so that it’s only driving the engine as fast as necessary for the speed of traffic, thus saving a lot of brake pads and a ton of gas!
Because most applications operate at a variety of load points, a motor with a drive can yield tremendous energy savings. Combining a motor with a drive in applications with variable loads can effectively increase the energy savings by 20 percent and as much as 60 percent in some applications.
These two concepts—variable speed capability and system efficiency—are the keys to reducing energy use. Since not every drive and motor combined will result in optimal savings, NEMA Member companies worked closely with the international community to create a Standard that establishes a system efficiency classification, the International Efficiency of Systems (IES). Basically, this helps users select a combination motor-drive system, usually referred to as a power drive system (PDS), or pair a motor with a drive (referred to as a complete drive module), and know how it will perform in an application, across virtually any load point.
This helps system designers and users get to what everyone wants: real energy savings.
NEMA will drive this solution by updating the NEMA Premium program to support system efficiency classifications. Over the next several months, you can expect to see more motors, drives, and PDSs entering the market from the best manufacturers in the business with both a NEMA Premium mark and an IES classification. This will give users and installers the confidence they need that they are actually saving the most energy possible across the entire range of use in the application.
Look for updates by visiting www.nema.org/nema-premium.